Risk-based.
Justified Limits.
Digital Cleaning Validation.
ValGenesis iClean™ streamlines cleaning validation with global standardization, automated oversight, and scientific justification—ensuring audit readiness across all sites.
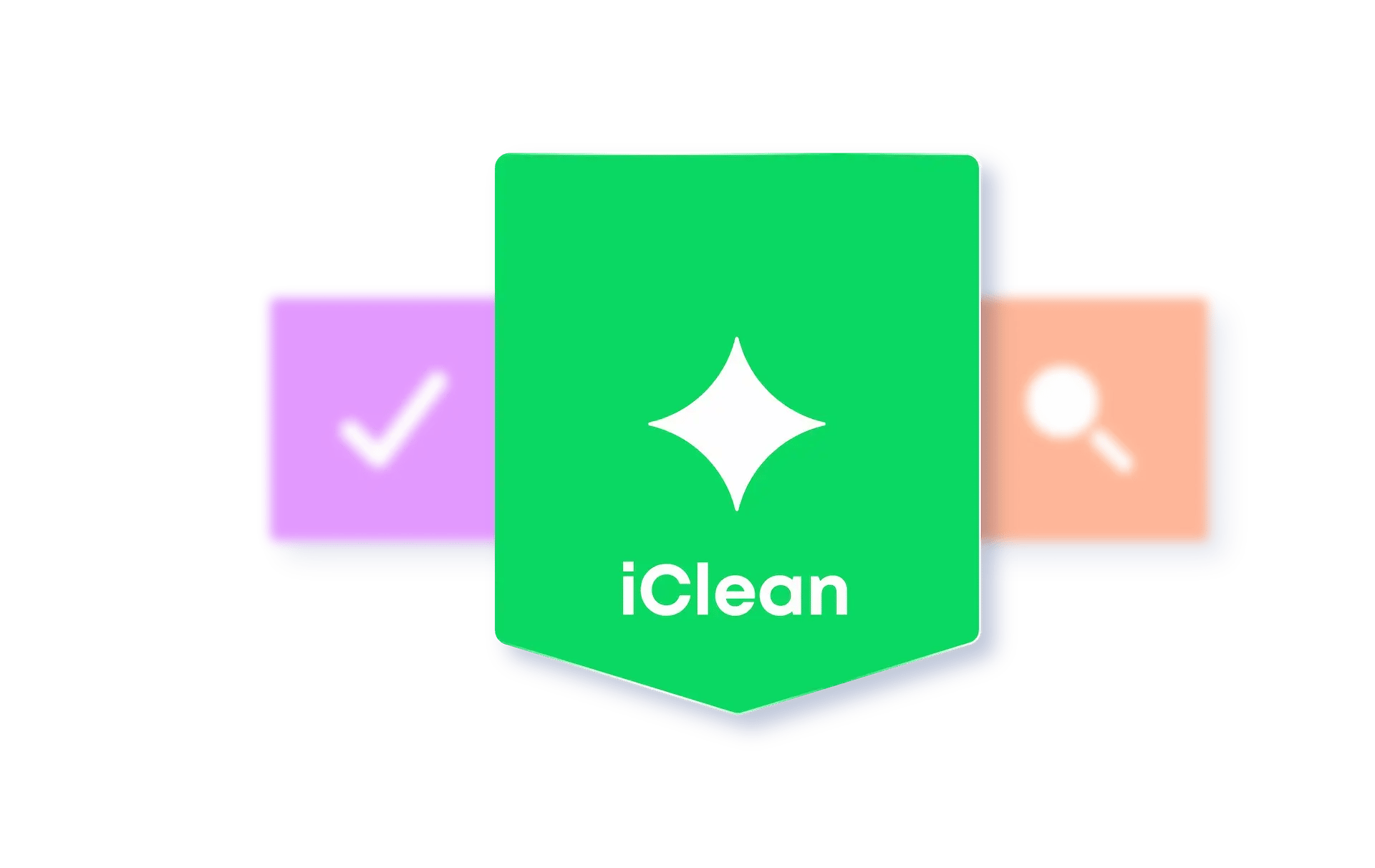
Using our Application
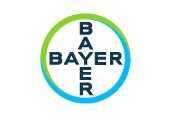
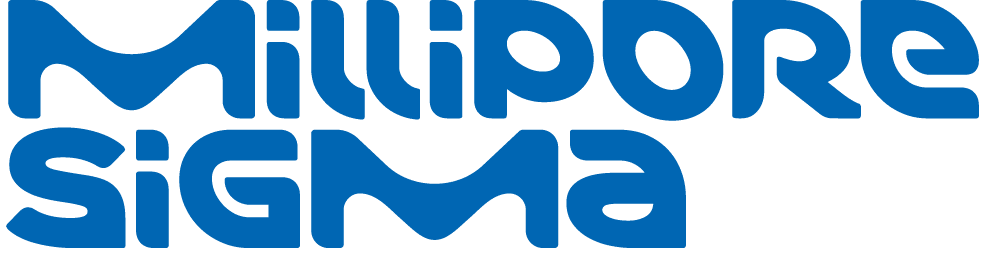
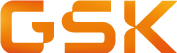
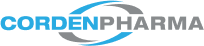
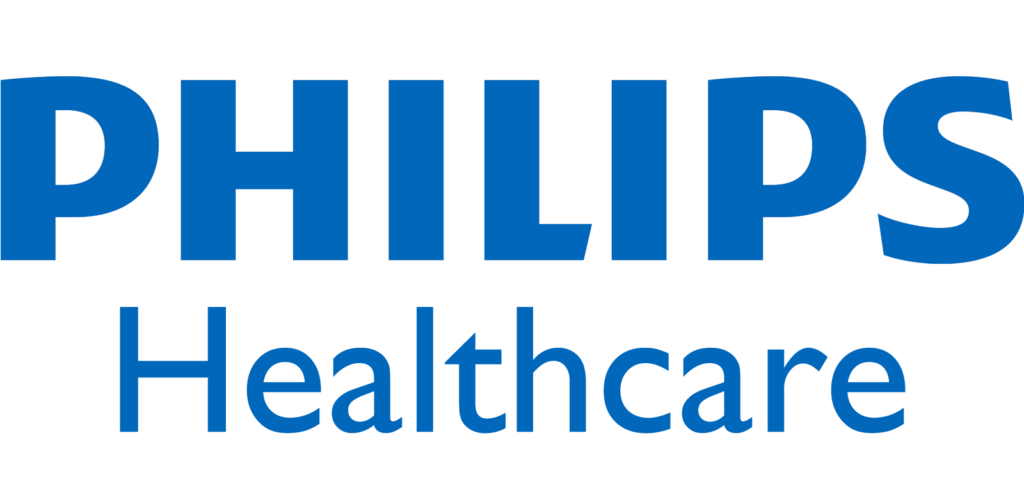
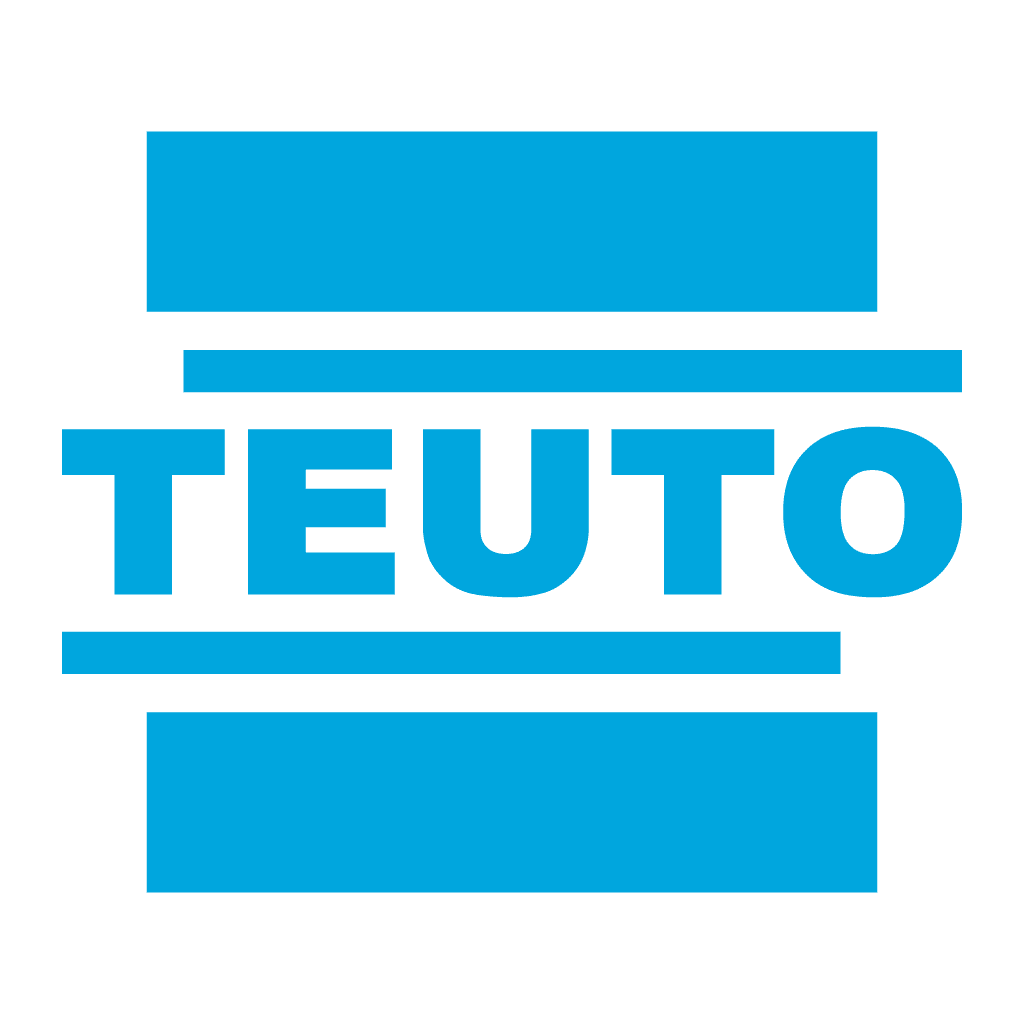
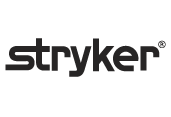
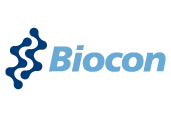

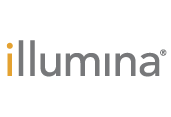
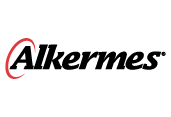
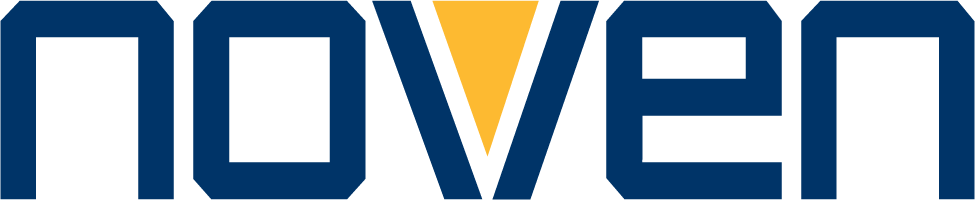
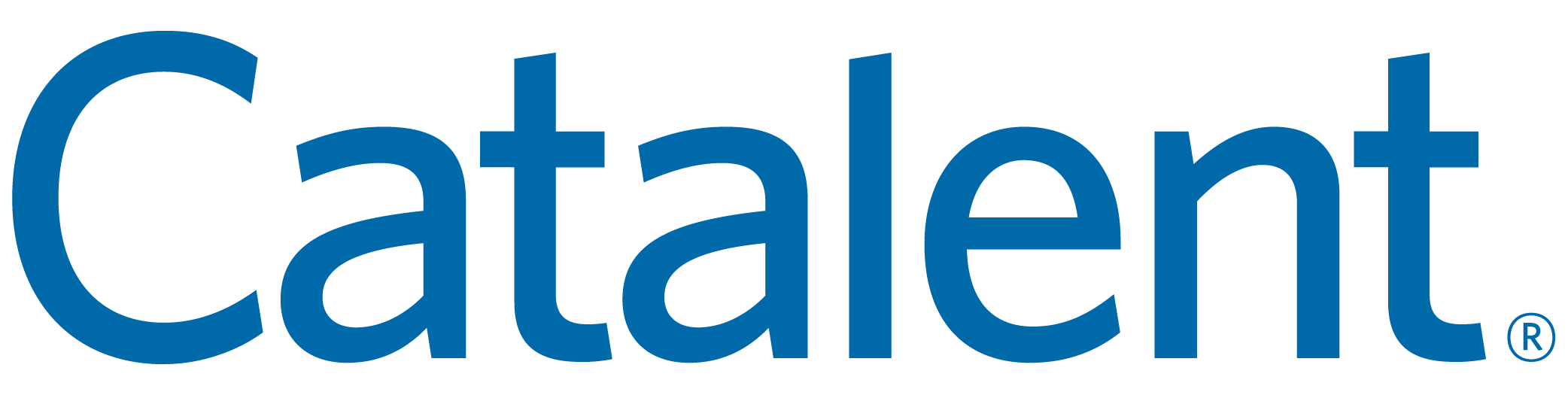
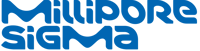
We chose ValGenesis because they were a known and trusted vendor. We had limited time and resources, and we knew the quicker we could implement the solution, the sooner we’d start realizing value from it.
Joshua Pelina
Validation Engineer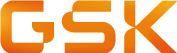
We work with ValGenesis iCMC to digitalize our QbD framework within GSK for the development of new vaccines. We are confident that iCMC will be key for simplification, acceleration, and knowledge management.
Hervé Gressard
Head of Global Project Statistics CMC Technical R&D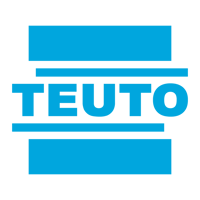
Implementing ValGenesis iCPV has transformed our approach to CPV. The integration of our data systems and the comprehensive training from the ValGenesis team have empowered our users, ensuring we meet regulatory standards while enhancing efficiency and data integrity.
Patricia Watanabe
Validation Supervisor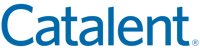
Working with ValGenesis was great. They helped us align the system with our new CSV program and uncover opportunities for process improvements and efficiency gains to maximize value.
Jeff Onis
Global IT Data Integrity Manager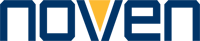
Our ERP upgrade would touch every department in the company. This was the ideal opportunity to transition from paper-based to digital validation, and now we’re reaping the benefits: signoff documents organized in one place, simplified review and approval, no more issues deciphering handwriting, one-click access to deviation reports, reduced printing costs—all totaling up to a successful outcome.
Mabel Santana
Compliance Manage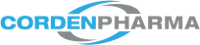
When we decided to go with iCMC, we wanted to have the roll-out concluded within six months. The support we received from the team, their willingness to accommodate our requests and timelines, and their expertise in resolving all the issues that came up during the project was amazing.
Dr. Iris Ziegler
Director QbD & Pharmaceutical SciencesImpact Metrics
digital documentation and traceability with automated audit trails
faster cleaning validation cycle time through automation
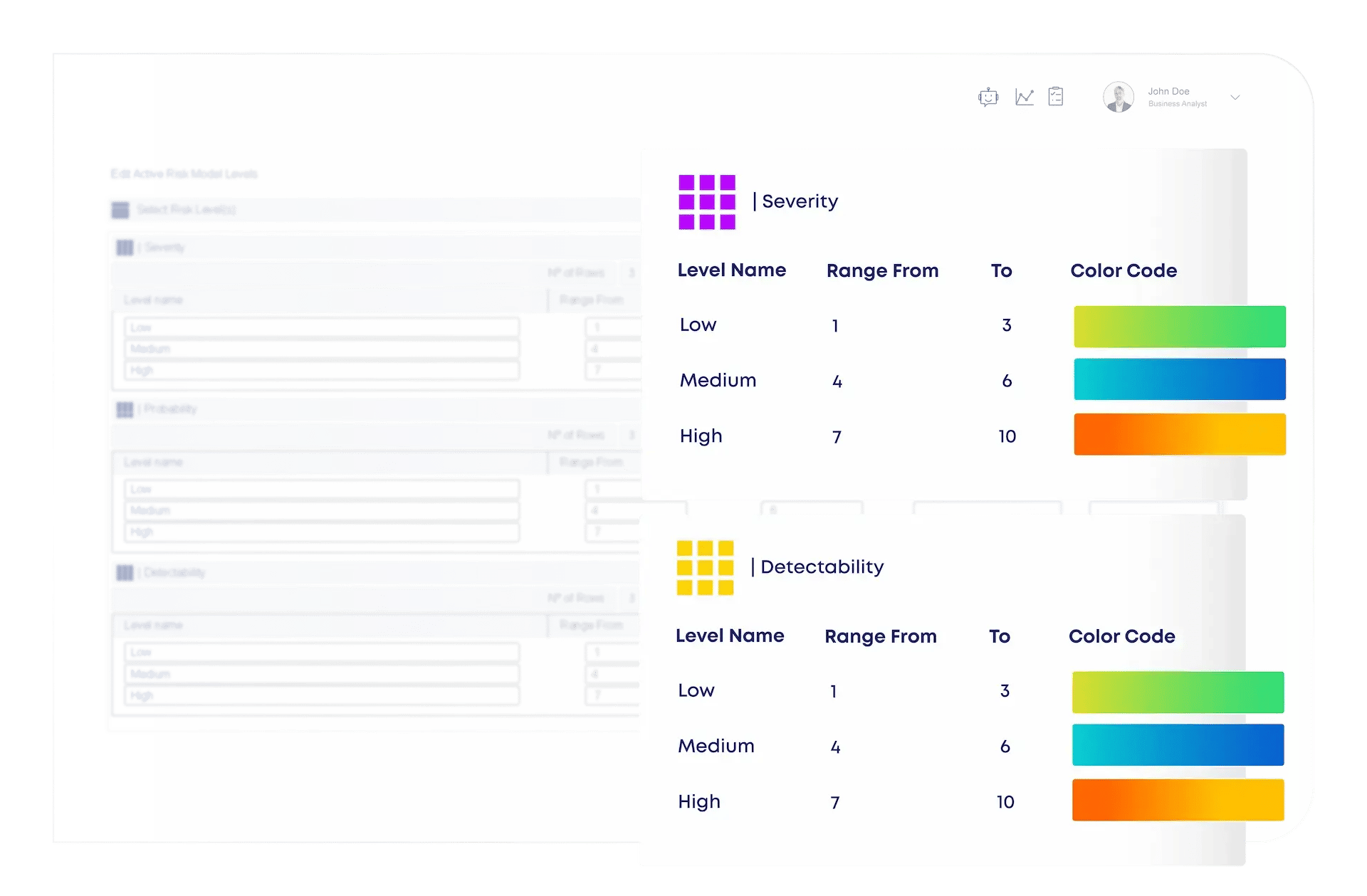
Discover How iClean Works as Part of Our Validation Lifecycle Suite
iClean digitalizes the entire cleaning validation lifecycle—from risk-based planning and MACO determination to execution and ongoing requalification. It automates calculations, integrates ADE/NOAEL-based scientific data, and uses 2D/3D equipment mapping to guide the sampling strategy.
With business-rule-driven decision trees, built-in residual limit enforcement, and a centralized method and agent repository, iClean helps teams reduce manual work, eliminate errors, and maintain global consistency. Its change control and requalification workflows ensure sustained compliance—even as processes evolve.
Overview
Accelerate compliance, reduce risk
Automate MACO calculations, validation cycles, and documentation for faster, inspection-ready delivery.
Standardize globally, flex locally
Centralize cleaning strategies while adapting validation protocols to site-specific and equipment-specific requirements.
Gain real-time oversight
Visualize status, risks, and readiness across sites through built-in analytics and intelligent dashboards.
Resources
Webinar
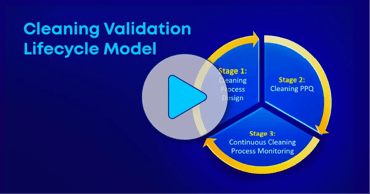
Digitization of Cleaning Validation Life ...
Cleaning Validation is a complex process. Over the years, the industry has ...
WatchWebinar
/Thumbnail%20-%20Webinar%20-%20Digitization%20of%20Cleaning%20Validation%20Lifecycle.webp?length=370&name=Thumbnail%20-%20Webinar%20-%20Digitization%20of%20Cleaning%20Validation%20Lifecycle.webp)
Digital Cleaning Validation Lifecycle
Cleaning validation is a complex process. Using manual, paper- or ...
WatchWebinar
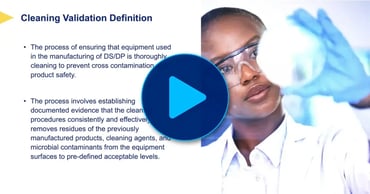
Managing Cleaning Validation at an ...
Ensuring the validated state of a cleaning process in an operational ...
WatchWebinar
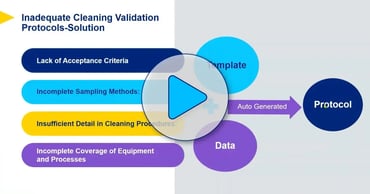
Common FDA 483 Cleaning Validation ...
The pharmaceutical industry continues to face challenges in maintaining ...
WatchWebinar
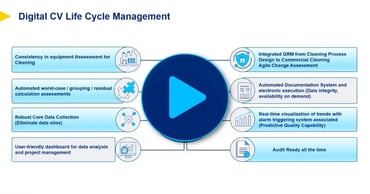
ValGenesis Process Manager: The Future of ...
The current pharma and biopharma business environment requires operational ...
WatchWebinar
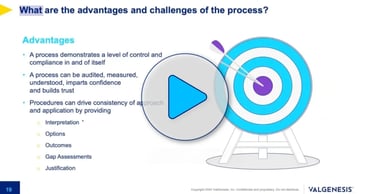
Cleaning Validation Programmes: Establishing ...
In the pharmaceutical industry, establishing an effective Cleaning ...
WatchWebinar
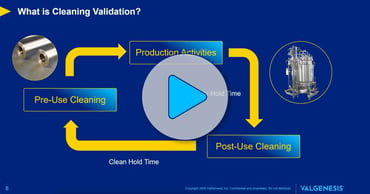
Digitize with Precision: Mastering Carry ...
Cleaning validation is often treated as an afterthought in pharmaceutical ...
WatchWebinar
.webp?length=370&name=Webinar-Thumbnail%20(5).webp)
Manufacturing Bottlenecks: Why Analog ...
Cleaning validation programs are complex to plan and deliver due to the ...
WatchFrequently Asked Questions
Do you need help with something or have questions about any features?
Ready for Smarter Cleaning Validation?
Simplify cleaning validation. Ensure audit readiness. Get started with ValGenesis iClean™.